Знаменитая строчка из «Юн Йе Фу» Цзинь Цао Пи, изображающая сцену производства плавки и литья под давлением в древнем Китае, гласит: «Плавка камня как инструмента и установка тысячи печей вместе». В древних методах обработки металлов в Китае литье под давлением играло заметную роль и имело широкое социальное влияние. Такие идиомы, как «модель», «керамика», «плавление и литье под давлением» и «соответствие», продолжали использовать терминологию отрасли литья под давлением. Трудящиеся создали традиционные методы литья под давлением с китайскими национальными особенностями благодаря многолетней производственной практике, передаваемой из поколения в поколение. Среди них наиболее важными являются глиняные формы, чугунные формы и литье по выплавляемым моделям, известные как три основных древних метода литья под давлением.
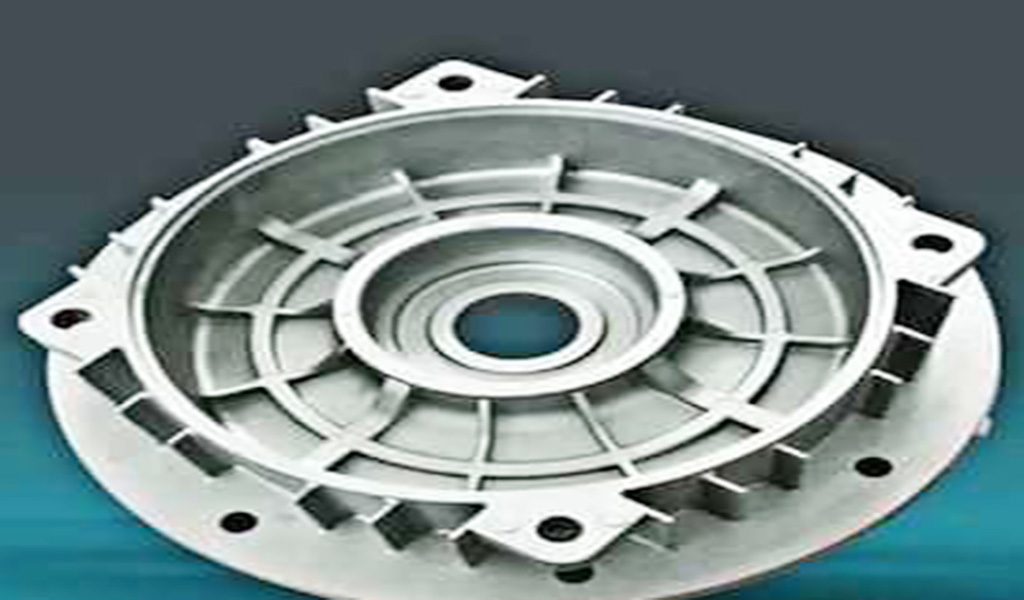
Литье под давлением в глиняных формах
Первоначальной техникой литья под давлением было использование каменных форм. Из-за сложности обработки камня и его неспособности выдерживать высокие температуры с развитием гончарного производства вместо него стали использовать глиняные формы. За более чем три тысячи лет до современного литья под давлением литье в глиняные формы всегда было одним из наиболее важных методов литья под давлением.
Литье под давлением в глиняных формах
Первоначальной техникой литья под давлением было использование каменных форм. Из-за сложности обработки камня и его неспособности выдерживать высокие температуры с развитием гончарного производства вместо него стали использовать глиняные формы. За более чем три тысячи лет до современного литья под давлением литье в глиняные формы всегда было одним из наиболее важных методов литья под давлением.
Краткое введение
Литье под давлением занимает видное место в технологии обработки металлов древнего Китая и имеет огромное социальное влияние. Лексика «модель», «расплав», «глиняная модель» и другие слова, которые мы сегодня часто используем в нашей повседневной жизни, происходят из терминологии древнего литейного производства. В древнем Китае рабочие создали два традиционных метода литья под давлением, метод моделирования гончарных изделий и метод выплавляемого воска, в своей многолетней производственной практике.
Процесс литья глины под давлением
- Изготовление пресс-форм
Вылепить из глины формы по прототипу предмета;
- Опрокидывание
Разбейте равномерно смешанную почву в плоские глиняные листы, прижмите их к внешней стороне глиняной формы и плотно прижмите, чтобы узоры глиняной формы отпечатались на глиняных пластинах. После того, как куски грязи наполовину высохнут, разрежьте их ножом на несколько частей в соответствии с ушами, ступнями, пальцами ног, дном, краями, углами или точками симметрии объекта. Затем сделайте треугольные врезные и шиповые соединения для двух соседних кусков глины и высушите их на воздухе или запеките на слабом огне, чтобы подровнять и восстановить узоры на внутренней поверхности форм. Это становится внешней формой, используемой для литья под давлением;
- Внутренний стандарт
Соскоблите тонкий слой грязевой формы, которая использовалась для изготовления внешней формы, пока она влажная, а затем высушите его над теплом, чтобы сделать внутреннюю форму. Толщина соскоба — это толщина отлитой медной посуды;
- Соответствие
Переверните внутреннюю форму на основание, а затем поместите внешний блок формы вокруг внутренней формы. После того, как внешняя модель закрыта, на ней остается закрытая модельная крышка, а на модельной крышке остается хотя бы одно сливное отверстие;
- Литье под давлением
Залейте раствор расплавленной бронзы вдоль разливочного отверстия, подождите, пока медная жидкость остынет, разбейте внешнюю форму, удалите внутреннюю форму и выньте отлитую медную посуду. После полировки и отделки красивое бронзовое изделие готово.
Метод раздельного литья под давлением как основной принцип процесса
При изготовлении бронзовых сосудов сложной формы древние также использовали метод литья под давлением в качестве основного принципа процесса для получения сосудов сложной формы. Как вариант, сначала отливают корпус сосуда, а затем заливают в верхнюю форму аксессуары (например, головы животных, столбы и т. д.); В качестве альтернативы, аксессуары (например, уши и ножки штатива) могут быть отлиты первыми, а затем граница может быть отлита во время заливки корпуса сосуда. Знаменитый «Четыре овцы Цзун» (найденный в Нинсяне, провинция Хунань) был отлит методом литья под давлением.
Раздельное литье под давлением
При изготовлении бронзовых сосудов сложной формы древние также использовали метод литья под давлением в качестве основного принципа процесса для получения сосудов сложной формы. Как вариант, сначала отливают корпус сосуда, а затем заливают в верхнюю форму аксессуары (например, головы животных, столбы и т. д.); В качестве альтернативы, аксессуары (например, уши и ножки штатива) могут быть отлиты первыми, а затем граница может быть отлита во время заливки корпуса сосуда. Знаменитый «Четыре овцы Цзун» (найденный в Нинсяне, провинция Хунань) был отлит методом литья под давлением.
Происхождение из ранней династии Шан
Происхождение этого метода можно проследить до периода Эрлиган (ранняя династия Шан) и периода Сяотун (поздняя династия Шан), и основная форма уже примерно установлена.
Весенне-осенний период стал основным направлением раздельного литья под давлением.
Сначала аксессуары для литья под давлением, а затем литье под давлением корпуса стали основным методом отдельного литья под давлением. Большинство изделий И в Синьчжэне, а также треножники и горшки в период Воюющих царств были отлиты таким образом. Успешное применение простых принципов процесса для решения сложных технологических проблем, использование простоты для противодействия сложности и демонстрация уникального мастерства в обычном труде — выдающееся творение древних рабочих, а также ключ к пониманию технологии литья под давлением бронзы Шан и Чжоу. посуда. Нереально ошибочно принимать сложные объекты, такие как Будда с четырьмя овцами, за отлитые под давлением восковые модели, и еще более неправильно делать бронзовые сосуды Шан и Чжоу загадочными и непреодолимыми.
Укладка литья под давлением
Еще одним выдающимся достижением древнекитайского литья под давлением в глиняные формы является раннее появление и широкое применение метода литья под давлением в стопку. Так называемое многослойное литье под давлением относится к сборке множества блоков формы или пар частей формы, которые заливаются через общий желоб, в результате чего одновременно получаются десятки или даже сотни отливок. Стоимость относительно невелика и до сих пор широко используется. Самое раннее литье под давлением с перекрытием в Китае — это монета Ци Дао периода Сражающихся царств, которая сделана из медных формовочных коробок с высокой симметрией и взаимозаменяемостью. Каждые две части объединены в один слой, который состоит из нескольких слоев. Во времена династии Хань он широко использовался в производстве монет, колесниц и лошадей. В последние годы в таких провинциях, как Шэньси, Хэнань и Шаньдун, были обнаружены такие печи для литья под давлением и печи для обжига. В частности, на месте плавки и литья под давлением династии Хань в деревне Сичжаосянь, уезд Вэнь, провинция Хэнань, было извлечено более 500 комплектов форм для литья под давлением 16 типов и 36 спецификаций, что дало нам ценную физическую информацию для понимания этого процесса. Они продуманно сконструированы и тонко обработаны, а толщина внутреннего литника составляет всего 2–3,5 миллиметра, что облегчает очистку литья под давлением. Отливки, отлитые с использованием этих форм, имеют пять уровней чистоты поверхности (всего четырнадцать уровней). Выход металла может достигать 90%, а технологический уровень близок к уровню аналогичных методов, применяемых в наше время в Фошане, провинция Гуандун.
Технология литья под давлением с вентилятором имеет долгую историю в Китае.
Начиная с периода позднего неолита Китай вступил в эпоху энеолита. Ранние артефакты из меди, обнаруженные в Таншане и других местах провинции Хэбэй, в том числе полученные путем ковки и плавления, указывают на то, что технология литья под давлением имеет долгую историю в Китае и развивалась очень рано.
В древней литературе есть много записей о Кунву (племя династии Ся, проживающее на севере современного города Дуян, провинция Хэнань), занимающееся гончарным делом и литьем меди под давлением, а также легенды о литье под давлением Юй Девяти котлов. Из недавних археологических раскопок видно, что династия Ся умела плавить и отливать бронзу. В первоначальной форме использовались каменные формы. Из-за сложности обработки камня и его неспособности выдерживать высокие температуры, на основе передовых технологий гончарного дела быстро стали использовать глиняные формы. На протяжении более 3000 лет, до появления современного машиностроения и использования литья под давлением в песчаные формы, это всегда было основным методом литья под давлением.
В начале династии Шан место Эрлитоу в Яньши, провинция Хэнань, использовалось в качестве символа, и небольшие производственные инструменты, такие как медные тесла и долота, уже отливались с использованием глиняных форм, а также повседневная утварь, такая как медные колокольчики и бронзовые дворяне. Позже, с символом Эрлигана в Чжэнчжоу, начала развиваться промышленность по выплавке бронзы и литью под давлением. Два больших котла, обнаруженные в Чжанчжае, Чжэнчжоу, весом 64,25 кг и 82,25 кг соответственно, указывают на то, что технология литья меди под давлением в середине династии Шан достигла значительного уровня, от одностороннего и двустороннего литья под давлением до возможности использования несколько форм и стержней для формирования композитных форм для литья крупных отливок весом более ста килограммов.
После того, как Пань Гэн переехал в Инь, технология плавки бронзы и литья под давлением достигла своего пика, отмеченного руинами Инь в Сяотуне, Аньян. Десятки тысяч артефактов из бронзы Шан и Чжоу, обнаруженных и переданных из поколения в поколение, являются не только важными историческими реликвиями, но и кристаллизацией мудрости и таланта рабов-плавильщиков. Их академическая, художественная ценность и технический уровень общепризнаны.
Для получения отливок из бронзы сложной формы и изысканного рисунка древние мастера плавки и литья под давлением применяли ряд важных технологических приемов.
Например, при приготовлении формовочных материалов отбираются местные материалы, а для рафинирования отбираются чистые песок и шлам с высокой огнестойкостью. Поверхностный ил, используемый для поверхности формы, промывается водой для получения очень мелкой и чистой глины (глины). Эта глина обладает хорошей пластичностью и прочностью, позволяет добиться высокой четкости и точности при переворачивании формы. Обратный шлам состоит из относительно крупного ила или смешивается с песком и растительным материалом, чтобы уменьшить расход осветленного шлама и повысить проницаемость формы для литья под давлением. Все грязевые материалы должны подвергаться длительной сушке в тени, многократным метаниям и подметаниям, чтобы они были высокоравномерно приготовлены и не трескались при формовании или высыхании.
Зрелое мастерство
Для сушки, обжига и сборки сердцевины формы, одинаковой толщины стенок для достижения одновременного затвердевания и предварительного нагрева формы для обеспечения гладкой заливки во времена династий Шан и Чжоу был изучен полный набор зрелых процессов, которые не только заложили техническая основа для будущих поколений литья в глиняные формы, а также для металлических форм и литья по выплавляемым моделям.
Однако при том социальном условии, что эксплуататорский класс владеет средствами производства и овладевает государственной машиной, научно-технические достижения трудящихся всегда захватываются правителями, которые используются для подавления и обмана народа и удовлетворения его упаднического и экстравагантные жизненные потребности. Среди бронзовых артефактов династий Шан и Чжоу четыре категории ритуальных, музыкальных, военных и колесниц составляли подавляющее большинство с небольшим количеством производственных инструментов. Многие артефакты династии Мин (сопровождающие погребальные предметы) после отливки были закопаны под землю. Такое положение сильно тормозит развитие общественной производительности. В результате более тысячи лет литье в глиняные формы в основном оставалось в стадии разового литья, и только в весенне-осенний период медные орудия (кирки) отливались многотипно (полупостоянные глиняные формы). .
Использование глиняных форм для отливки больших и негабаритных отливок претерпело значительные изменения со времен династий Тан и Сун. Железный лев Пяти династий в Цанчжоу, железная башня династии Северная Сун в Данъяне и колокол династии Мин в храме Большого Колокола в Пекине — всемирно известные гигантские отливки. В томе 8 книги Сун Инсин «Небесные творения» описываются два способа отливки больших кусков: один — отливать их один за другим в многорядных печах (часы в пределах килограмма), а другой — отливать их в нескольких печах (десять тысяч часов). колокола). В технологических условиях древнего кустарного производства это, надо сказать, умный и искусный процесс, требующий умелых навыков, хорошей организации и слаженности. Даже в наше время успешно отлить от 30 до 40 тонн крупных отливок — непростая задача.
В начале династии Шан в Китае отливали глиняные модели, и он достиг своего пика в середине династии Шан. Таким образом, древние мастера создали беспрецедентные сокровища, такие как Simuwu Ding и Four-козла Квадрат Zun.
Зрелое мастерство
Для сушки, обжига и сборки сердцевины формы, одинаковой толщины стенок для достижения одновременного затвердевания и предварительного нагрева формы для обеспечения гладкой заливки во времена династий Шан и Чжоу был изучен полный набор зрелых процессов, которые не только заложили техническая основа для будущих поколений литья под давлением в глиняные формы, а также для литья под давлением в металлические формы и по выплавляемым моделям.
Однако при том социальном условии, что эксплуататорский класс владеет средствами производства и овладевает государственной машиной, научно-технические достижения трудящихся всегда захватываются правителями, которые используются для подавления и обмана народа и удовлетворения его упаднического и экстравагантные жизненные потребности. Среди бронзовых артефактов династий Шан и Чжоу четыре категории ритуальных, музыкальных, военных и колесниц составляли подавляющее большинство с небольшим количеством производственных инструментов. Многие артефакты династии Мин (сопровождающие погребальные предметы) после отливки были закопаны под землю. Такое положение сильно тормозит развитие общественной производительности. В результате более тысячи лет литье в глиняные формы в основном оставалось в стадии одноразового литья под давлением, и только в весенне-осенний период медные орудия (кирки) отливались многотипными (полупостоянные глиняные формы).
Использование глиняных форм для литья больших и негабаритных отливок под давлением претерпело значительные изменения со времен династий Тан и Сун. Железный лев Пяти династий в Цанчжоу, железная башня династии Северная Сун в Данъяне и колокол династии Мин в храме Большого колокола в Пекине — всемирно известные гигантские отливки под давлением. В томе 8 книги Сун Инсин «Небесные творения» описываются два способа отливки больших кусков: один — отливать их один за другим в многорядных печах (часы в пределах килограмма), а другой — отливать их в нескольких печах (десять тысяч часов). колокола). В технологических условиях древнего кустарного производства это, надо сказать, умный и искусный процесс, требующий умелых навыков, хорошей организации и слаженности. Даже в наше время успешно отлить от 30 до 40 тонн больших отливок под давлением — непростая задача.
В начале династии Шан в Китае было литье под давлением глиняных моделей, и он достиг своего пика в середине династии Шан. Таким образом, древние мастера создали беспрецедентные сокровища, такие как Simuwu Ding и Four-козла Квадрат Zun.
Литье металла под давлением
Краткое введение
Литье металла под давлением — это процесс плавления металла в жидкость, отвечающую определенным требованиям, и заливка его в форму. После охлаждения, затвердевания и очистки получается отливка с заданной формой, размером и характеристиками. литье под давлением грубых зародышей из-за их близкого формирования позволяет избежать механической обработки или минимальной обработки, снизить затраты и в некоторой степени сократить время. Литье под давлением является одним из основных процессов в современном машиностроении.
Классификация
Виды и методы моделирования литья металлов под давлением принято делить на:
① Обычная литье под давлением в песчаные формы включает три типа: мокрая песчаная форма, сухая песчаная форма и химически затвердевшая песчаная форма.
② Специальное литье под давлением можно разделить на два типа в зависимости от формовочных материалов: специальное литье под давлением с природным минеральным песком и гравием в качестве основного формовочного материала (например, литье под давлением, литье под давлением, литье под давлением в оболочке в цехах литья под давлением, отрицательное литье под давлением, литье под давлением в полную форму, литье под давлением в керамической форме и т. д.) и специальное литье под давлением с использованием металла в качестве основного формовочного материала (например, литье под давлением в металлической форме, литье под давлением, непрерывное литье под давлением, литье под низким давлением, центробежное литье под давлением и др.).
Процесс литья под давлением в песчаные формы
Процессы литья металлов под давлением обычно включают:
- Подготовка форм для литья под давлением (контейнеры, которые превращают жидкие металлы в твердые отливки), которые можно разделить на песчаные формы, металлические формы, керамические формы, грязевые формы, графитовые формы и т. д. в зависимости от используемых материалов и могут быть разделены в одноразовые формы, полупостоянные формы и постоянные формы в зависимости от количества использований. Качество подготовки формы для литья под давлением является основным фактором, влияющим на качество литья под давлением;
- Плавка и разливка литых металлов, в том числе чугуна, стального литья и литья цветных сплавов;
- обработка и проверка литья под давлением, включая удаление посторонних предметов на сердечнике и поверхности литья под давлением, удаление литья под давлением и стояка, соскабливание и шлифование заусенцев и заусенцев, а также термообработку, формование, обработку для предотвращения ржавчины, и черновая обработка.
История
В древности в Китае, Индии, Вавилоне, Египте, Греции и Риме уже отливали оружие, жертвенные сосуды, произведения искусства и домашнюю утварь. Ранние отливки изготавливались из золота, серебра, меди и их сплавов. Бронзовый век — славная страница в истории человеческой цивилизации; В дальнейшем снова появились чугунные детали. Литье под давлением из железа широко использовалось в Китае еще в период Воюющих царств с давними технологическими традициями. Прилагаемый рисунок представляет собой схему котла для литья под давлением в «Tiangong Kaiwu» (см. История металлургии). Литье металла под давлением
Металлургия и литье под давлением являются взаимодополняющими технологическими процессами, и термин «плавка и литье под давлением» в древнем Китае отражает этот факт. Хотя в более поздние времена литейная технология превратилась в относительно самостоятельную отрасль технологии механического производства, она до сих пор неотделима от металлургической технологии.
① Чугун имеет долгую историю, но скорость его разработки низкая. Лишь в 1722 году Леомир создал «купол» и начал изучать микроструктуру и поверхность излома чугуна под микроскопом, когда ситуация изменилась. В 1734 г. был опубликован «De ferro» Сведенберга, давший предварительное теоретическое представление о технологии чугуна. С 1765 по 1785 год, в связи с появлением паровой машины, чугун широко использовался в машиностроении с 1860-х годов, а в транспортном секторе также использовались чугунные рельсы. В 1788 году для Парижского водопровода было изготовлено общей протяженностью 60 км чугунных труб для подачи воды. Растущий спрос на чугун способствовал техническому прогрессу и теоретическим исследованиям чугуна.
К литейным свойствам металлов относятся:
- Ликвидность, способность жидкого металла заполнять форму;
- Тенденция к усадке, большая объемная усадка от жидкости к твердому, склонность к дефектам, таким как усадочные полости, и большая усадка линейного размера, влияющая на окончательную точность размеров литья под давлением;
- Склонность к горячему растрескиванию, некоторые металлы и сплавы склонны к растрескиванию и расслоению в процессе литья под давлением (см. затвердевание металлов).
Литье под давлением
История
Литье по выплавляемым моделям в Китае зародилось не позднее весеннего и осеннего периода. Бронзовый запрет периода Весны и Осени, обнаруженный в гробнице № 2 Чу в Сяси, Сичуань, провинция Хэнань, является самым ранним литьем под давлением по выплавляемым моделям, известным до сих пор. Этот бронзовый запрет украшен резными узорами облаков со всех четырех сторон и сторон, с двенадцатью стоящими зверями вокруг него и в общей сложности десятью стоящими ногами зверей под ним. Сложность и разнообразие ажурных узоров, великолепный и торжественный внешний вид отражают то, что литье по выплавляемым моделям в Китае было относительно зрелым в середине периода Весны и Осени. После периода Воюющих царств и династий Цинь и Хань литье по выплавляемым моделям стало более популярным, особенно во времена династий Суй и Тан до династий Мин и Цин, литье по выплавляемым моделям в основном использовалось для отливки бронзовых изделий.
Литье по выплавляемым моделям обычно используется для изготовления небольших отливок под давлением.
Медная посуда, отлитая этим методом, не имеет следов форм и следов прокладок, и ее лучше использовать для литья полых изделий. Традиционная технология литья под давлением в Китае оказывает значительное влияние на мировое металлургическое развитие. Прецизионное литье под давлением в современной промышленности разработано на основе традиционного литья под давлением по выплавляемым моделям. Хотя существуют значительные различия в восковых материалах, формовочных материалах и используемых методах обработки, их принципы обработки одинаковы. В середине 1940-х годов, когда Остин, американский инженер, основал современную технологию литья под давлением, названную в его честь, он черпал вдохновение в традиционном китайском литье под давлением по выплавляемым моделям. В 1955 году Остинская лаборатория подала петицию о первом литье под давлением по выплавляемым моделям, и японский ученый Лу Цайи возражал против того факта, что литье под давлением по выплавляемым моделям использовалось в истории Китая и истории Японии, и, наконец, выиграл судебный процесс. .
Литье по выплавляемым моделям
Литье под давлением, также известное как «литье под давлением с потерей воска», обычно относится к методу литья под давлением, при котором модель изготавливается из легкоплавкого материала, а на поверхность модели наносится несколько слоев огнеупорного материала для формирования оболочки формы. . Затем форму расплавляют и выгружают из оболочки формы, чтобы получить форму без поверхности разъема. После высокотемпературного обжига форму можно засыпать песком и залить. Из-за широкого использования восковых материалов для производства литье по выплавляемым моделям часто называют «литьем под давлением с выплавкой воска».
Типы сплавов, которые могут быть получены методом литья под давлением, включают углеродистую сталь, легированную сталь, жаропрочный сплав, нержавеющую сталь, прецизионный сплав, сплав с постоянными магнитами, подшипниковый сплав, медный сплав, алюминиевый сплав, титановый сплав и чугун с шаровидным графитом.
Форма отливок по выплавляемым моделям, как правило, относительно сложна: минимальный диаметр отверстий, которые можно отлить в отливках, достигает 0,5 мм, а минимальная толщина стенок отливок составляет 0,3 мм. В производстве некоторые компоненты, которые изначально состояли из нескольких частей, могут быть спроектированы как единое целое путем изменения структуры деталей и прямого литья по выплавляемым моделям, чтобы сэкономить время обработки и расход металлического материала, сделав структуру деталей более разумной.
Вес отливок по выплавляемым моделям в основном находится в диапазоне десятков ньютонов (т.е. от десятков граммов до нескольких килограммов). Производить тяжелые отливки методом литья под давлением сложнее, но в настоящее время вес производства крупных отливок под давлением достиг примерно 800 ньютонов.
Процесс литья под давлением сложен и трудно поддается контролю, а используемые и потребляемые материалы дороги. Поэтому он подходит для производства мелких деталей сложной формы, требующих высокой точности или сложных в обработке, таких как лопатки турбинных двигателей.
Изготовление инвестиционных форм
Первым процессом производства литья по выплавляемым моделям является изготовление выплавляемых форм, которые используются для формирования модели огнеупорной оболочки со средней полостью. Следовательно, для получения отливок под давлением с высокой точностью размеров и чистотой поверхности сама форма для выплавки должна иметь высокую точность размеров и чистоту поверхности. Кроме того, работа самой пресс-формы также должна быть максимально простой и пригодной для последующих процессов, таких как изготовление оболочек. Чтобы получить требуемую выше высококачественную выплавляемую форму, в дополнение к хорошему формованию (формам для прессования выплавляемых форм), также необходимо выбрать соответствующие материалы для изготовления форм (называемые материалами для форм) и разумные процессы изготовления форм.
Материал формы
Характеристики формовочных материалов должны не только обеспечивать удобное изготовление форм для выплавки с точными размерами, высокой чистотой поверхности, хорошей прочностью и малым весом, но и создавать условия для изготовления оболочек форм и получения качественных отливок. Материал формы обычно изготавливается из воска, натуральной смолы и пластика (синтетическая смола). Формы на восковой основе, которые в основном изготавливаются из воска, имеют более низкую температуру плавления 60-70 ℃; Любой материал для форм, в основном изготовленный из натуральной смолы, называется материалом для форм на основе смолы с немного более высокой температурой плавления около 70-120 ℃.
Подготовка и переработка формовочных материалов
1) Подготовка материалов формы
Целью подготовки материала формы является смешивание различного сырья, из которого состоит материал формы, в однородное целое и обеспечение того, чтобы состояние материала формы соответствовало требованиям прессования и плавления.
Во время приготовления нагревание в основном используется для плавления и смешивания различных сырьевых материалов в одно целое. Затем при охлаждении материал формы интенсивно перемешивают до состояния пасты для прессования расплавленных форм. Иногда бывают ситуации, когда материал формы плавится в жидкость и заливается прямо в форму.
2) Переработка материалов пресс-форм.
При использовании форм на основе смолы, в связи с высокими требованиями к качеству выплавляемых форм, новые материалы в основном используются для изготовления форм для прессования выплавляемых форм литья под давлением. Переработанный материал формы после извлечения из формы используется для изготовления формы для расплава системы литников и стояков после повторного плавления и фильтрации.
При использовании форм на основе воска материал формы, полученный после извлечения из формы, может быть переработан и использован для изготовления новых форм. Однако во время циклического использования характеристики материала формы будут ухудшаться, что приведет к повышению хрупкости, увеличению содержания золы, снижению текучести, увеличению скорости усадки и изменению цвета с белого на коричневый. В основном это связано с ухудшением качества стеариновой кислоты в материале формы. Следовательно, чтобы максимально восстановить первоначальные характеристики старого материала формы, необходимо удалить мыльные соли из старого материала формы. Общие методы включают обработку соляной кислотой (серной кислотой), обработку активированной глиной и электролитическое восстановление.
Изготовление инвестиционных форм и модулей
1) Изготовление инвестиционных форм
В производстве давление в основном используется для вдавливания материала пастообразной формы в форму для изготовления формы для расплава. Перед прессованием формы на поверхность формы необходимо нанести тонкий слой разделительного агента, чтобы удалить форму из формы. При прессовании модельного материала на основе воска разделяющим агентом может быть моторное масло, скипидар и т. д.; При прессовании форм на основе смолы в качестве разделительного агента обычно используется смесь кунжутного масла и спирта или силиконового масла. Чем тоньше слой разделительного агента, тем лучше, так что форма может лучше воспроизвести прессованную поверхность и улучшить гладкость поверхности формы. Существует три метода прессования расплавленных форм, а именно метод давления плунжера, метод давления воздуха и метод давления поршня.
2) Сборка пресс-форм
Сборка форм для выплавки представляет собой комбинацию форм для выплавки, которые образуют литье под давлением, и форм для выплавки, которые образуют систему литников и стояков. Существует два основных метода:
- Метод сварки использует тонкий кусок паяльника для плавления соединительных частей формы для плавления, так что форма для плавления сваривается вместе. Этот способ более распространен.
- При производстве небольших отливок по выплавляемым моделям в больших количествах метод механической сборки широко используется в зарубежных странах для объединения модулей. Использование этого типа модуля может значительно улучшить комбинацию модулей и эффективность, а также улучшить условия работы.
Изготовление формованных оболочек
Формы для литья по выплавляемым моделям можно разделить на два типа: сплошное тело и многослойная оболочка, и в настоящее время наиболее часто используемым типом является многооболочка.
После погружения модуля с огнеупорным покрытием обсыпьте его материалом, подобным огнеупорному материалу, а затем несколько раз высушите и отвердите, пока слой огнеупорного покрытия не достигнет необходимой толщины. Это формирует на модуле многослойную оболочку, которую обычно оставляют на некоторое время для полного затвердевания, а затем расплавляют модуль, в результате чего получается многослойная оболочка.
Некоторые многослойные оболочки необходимо упаковать и заполнить песком; Некоторые не нужно заливать сразу после обжарки.
Когда форма теряется во время плавления, оболочка будет подвергаться давлению со стороны увеличивающегося объема расплавленного материала формы; При обжиге и заливке различные части оболочки кристаллизатора будут испытывать взаимное защемление и неравномерное расширение и сжатие, поэтому металл также может подвергаться высокотемпературным химическим реакциям с материалом кожуха кристаллизатора. Таким образом, к оболочке предъявляются определенные требования к производительности, такие как малая скорость расширения и сжатия; Высокая механическая прочность, термостойкость, огнестойкость и химическая стойкость при высоких температурах; Оболочка формы также должна иметь определенную степень воздухопроницаемости, чтобы газ внутри оболочки формы мог плавно выходить во время заливки. Все они связаны с огнеупорными материалами, клеями и процессами, используемыми при изготовлении корпуса.
Материалы, используемые для изготовления корпусов пресс-форм
Материалы, используемые для изготовления корпусов пресс-форм, можно разделить на два типа. Один тип используется для непосредственного формирования оболочки пресс-формы, такой как огнеупорные материалы, клеи и т. д.; Другой тип — это материалы, используемые для получения качественных оболочек, упрощения операций и улучшения процессов, такие как флюсы, отвердители, поверхностно-активные вещества и т. д.
Огнеупорные материалы
В настоящее время огнеупоры, используемые при литье по выплавляемым моделям, в основном представляют собой кварц и корунд, а также алюмосиликатные огнеупоры, такие как огнеупорная глина, боксит, коксовый камень и т. д. Иногда также используются циркон, магнезия (MgO) и т. д.
связующее
Наиболее часто используемым связующим в литье под давлением по выплавляемым моделям является коллоидный раствор силиката (называемый золем силиката), такой как раствор гидролиза этилсиликата, жидкое стекло и золь кремнезема. Вещества, входящие в их состав, в основном представляют собой кремниевую кислоту (H2SiO3) и растворители, иногда со стабилизаторами, такими как NaOH в золе кремниевой кислоты.
Гидролизат этилсиликата — это самое раннее и наиболее часто используемое связующее в золь-гель литье под давлением кремниевой кислоты, полученное гидролизом этилсиликата; Оболочечная форма из жидкого стекла склонна к деформации и растрескиванию, а отливки, отлитые с ее помощью, имеют плохую точность размеров и чистоту поверхности. Однако в Китае при производстве отливок под давлением из углеродистой стали с более высокими требованиями к точности и отливок из цветных сплавов с более низкой температурой плавления жидкое стекло по-прежнему широко используется в производстве; Стабильность золя кремниевой кислоты хорошая, и он может храниться в течение длительного времени. При изготовлении оболочек формы нет необходимости в специализированных отвердителях, но золь кремнезема оказывает слабое смачивающее действие на форму. Процесс затвердевания оболочки пресс-формы представляет собой процесс сушки, который занимает много времени.
Процесс изготовления ракушки
Основными процессами и процессами в процессе изготовления скорлупы являются:
1) Обезжиривание и обезжиривание модулей
При использовании формовочных материалов на восковой основе для изготовления выплавляемых форм, чтобы улучшить способность покрытия смачивать поверхность модуля, необходимо удалить масляные пятна на поверхности модуля.
2) Нанесите покрытие и отшлифуйте модуль.
Перед нанесением покрытия его следует равномерно перемешать, чтобы свести к минимуму осаждение огнеупорных материалов в барабане для нанесения покрытия. Вязкость или удельный вес покрытия должны быть отрегулированы таким образом, чтобы покрытие могло хорошо заполнять и смачивать форму. При нанесении покрытия модуль следует погружать в покрытие и встряхивать вверх и вниз, чтобы покрытие хорошо смачивало форму и равномерно покрывало поверхность модуля. После нанесения покрытия шум можно рассеять.
3) Сушка и закалка скорлупы
После того, как каждый слой оболочки покрыт, его следует высушить и затвердеть, чтобы связующее в покрытии изменилось с золя на гель и гель и соединило огнеупорные материалы вместе.
4) Потеря расплава в самообразованной оболочке
После того, как оболочка полностью затвердеет, модуль необходимо выплавить из оболочки. Поскольку модуль обычно изготавливается из материалов на основе воска, этот процесс также называется депарафинизацией. В соответствии с различными методами нагрева существует множество методов депарафинизации, наиболее часто используемыми являются метод горячей воды и такой же метод пара под давлением.
5) Прокаленная скорлупа
Если требуется формовочная (пескоструйная) заливка, перед обжигом вынутую оболочку следует закопать в частицы песка внутри ящика, а затем загрузить в печь для обжига. Если скорлупа имеет высокую жаропрочность и не требует формовки и заливки, то скорлупу из формы можно сразу отправить в печь для обжига. Постепенно увеличивайте температуру печи во время обжига, нагревайте оболочку до 800-1000 ℃ и выдерживайте ее в течение определенного периода времени, прежде чем можно будет начать заливку.
Заливка отливок по выплавляемым моделям
Обычно используемые методы заливки для литья под давлением включают:
1) Существует несколько методов термического литья под давлением.
Это наиболее широко используемый вид заливки, при котором оболочка формы вынимается из обжиговой печи и разливается при высоких температурах. В этот момент металл медленно остывает в оболочке формы и может заполнить форму с высокой текучестью, поэтому литье под давлением может хорошо воспроизвести форму полости формы и повысить точность литья под давлением. Однако медленное охлаждение литья под давлением в горячей форме может вызвать укрупнение зерен, что снижает механические свойства литья под давлением. При заливке отливок из углеродистой стали поверхность отливок с более медленным охлаждением также склонна к окислению и обезуглероживанию, что снижает поверхностную твердость, гладкость и размерную точность отливок.
2) Заливка вакуумным отсосом
Поместите оболочку формы в вакуумную разливочную коробку и откачайте газ из полости через небольшие поры в оболочке формы, что позволит жидкому металлу лучше заполнить полость, воспроизвести форму полости, повысить точность литья под давлением и предотвратить появление дефектов. такие как отверстия для воздуха и недостаточная заливка. Этот метод применяется за рубежом.
3) Кристаллизация под давлением
Поместите оболочку формы в резервуар высокого давления для заливки. После завершения немедленно закройте резервуар под давлением и нагнетайте в резервуар воздух под высоким давлением или инертный газ, чтобы затвердеть литье под давлением, чтобы увеличить плотность литья под давлением. Максимальное давление за границей достигло 150 атм.
4) Направленная кристаллизация (направленное затвердевание)
Некоторые отливки по выплавляемым моделям, такие как турбинные лопатки, магнитная сталь и т. д., могут значительно улучшить свои рабочие характеристики, если их кристаллическая структура представляет собой столбчатые кристаллы, расположенные в определенном направлении. Поэтому технология направленной кристаллизации литья под давлением быстро развивается.